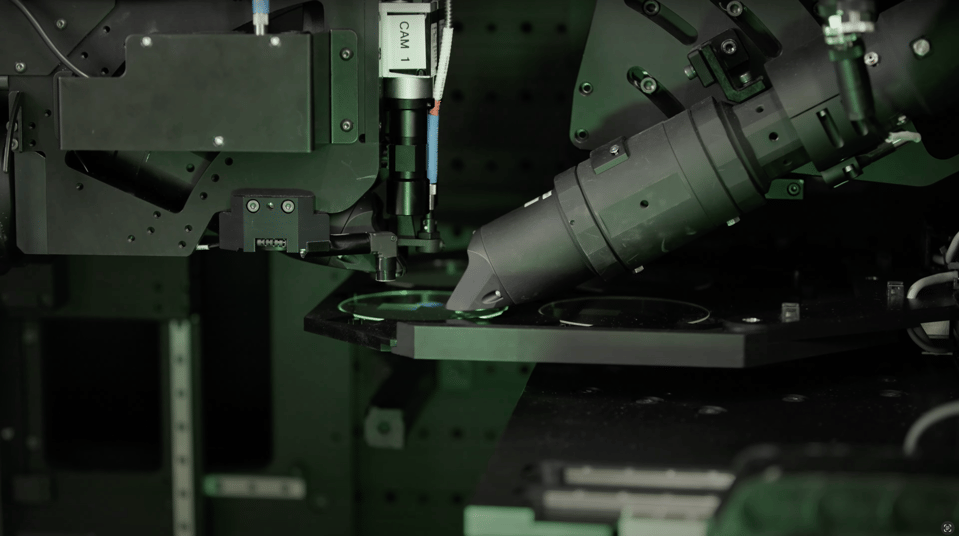
Blogs
Achieving Precise Optical Alignment for the Metrology System WG-IQ
In the world of metrology, achieving precise optical alignment is critical for accurate measurements and ensuring the reliability of the system. The WG-IQ metrology system is no exception, and it presents a unique challenge when it comes to aligning its camera, which is mounted on a 180° rotation stage. In this blog post, we will explore the innovative use of two autocollimators that enable the formation of a stable optical axis, making the optical alignment of the WG-IQ metrology system possible and efficient.
The WG-IQ Metrology System and Its Challenges
The WG-IQ metrology system features a camera mounted on a 180° rotation stage, allowing for a wide range of measurement applications. This configuration, however, poses a challenge for optical alignment. As the camera rotates on the stage, maintaining a consistent and precise optical axis is critical for accurate measurements. The difficulty lies in ensuring that the camera can always see the optical axis throughout its full range of motion.
Understanding Autocollimators
Caption: Figure 1 - Working principle of an autocollimator, demonstrating the imaging of angular displacement onto a sensor.
As seen in Figure 1, an autocollimator is an optical instrument that measures angular displacements with high precision. It emits and receives collimated light beams, which are perfectly parallel rays of light. When the collimated light is reflected by a reference surface, the autocollimator captures the reflected light and images it onto a sensor. The autocollimator's focal length (f) determines the relationship between the angular displacement of the reference surface (α) and the displacement of the image on the sensor (d). This relationship is given by the equation:
Digital autocollimators, which use cameras as sensors, can register tiny displacements of just a few micrometers. This allows them to achieve arcsecond accurate angle measurements with ease.
The Dual Autocollimator Solution
Caption: Figure 2 - Dual autocollimators forming a common optical axis and the camera's view of each autocollimator.
To address the challenge of aligning the WG-IQ metrology system's camera, two autocollimators, as depicted in Figure 2, are facing each other. They form a stable and fixed optical axis, which is crucial for precise alignment. The camera mounted on the 180° rotation stage can now "see" the optical axis created by the two autocollimators at all times. As the camera rotates, it maintains a constant line of sight with the optical axis, ensuring that the alignment remains accurate and consistent throughout the full range of motion.
How This Solution Benefits the WG-IQ Metrology System
This innovative use of dual autocollimators in the WG-IQ metrology system offers several key benefits:
-
Enhanced Precision: Forming a stable optical axis using two autocollimators allows for more accurate and consistent alignment, ultimately leading to more precise measurements.
-
Improved Efficiency: The dual autocollimator solution enables the camera to maintain a constant line of sight with the optical axis throughout its full range of motion. This reduces the need for time-consuming and complex alignment procedures, resulting in increased efficiency.
-
Versatility: The ability to maintain precise optical alignment while the camera is mounted on a 180° rotation stage opens up a wide range of potential applications and measurement scenarios.
Conclusion
The WG-IQ metrology system showcases the power of innovation in overcoming unique challenges, such as aligning a camera mounted on a 180° rotation stage. By employing two autocollimators facing each other to create a stable optical axis, WG-IQ is guaranteed to have an accurate and repeatable optical alignment. This innovative approach enhances measurement precision, improves efficiency, and expands the potential applications of the WG-IQ metrology system, demonstrating the importance of creative solutions in the field of optical metrology.
Written by