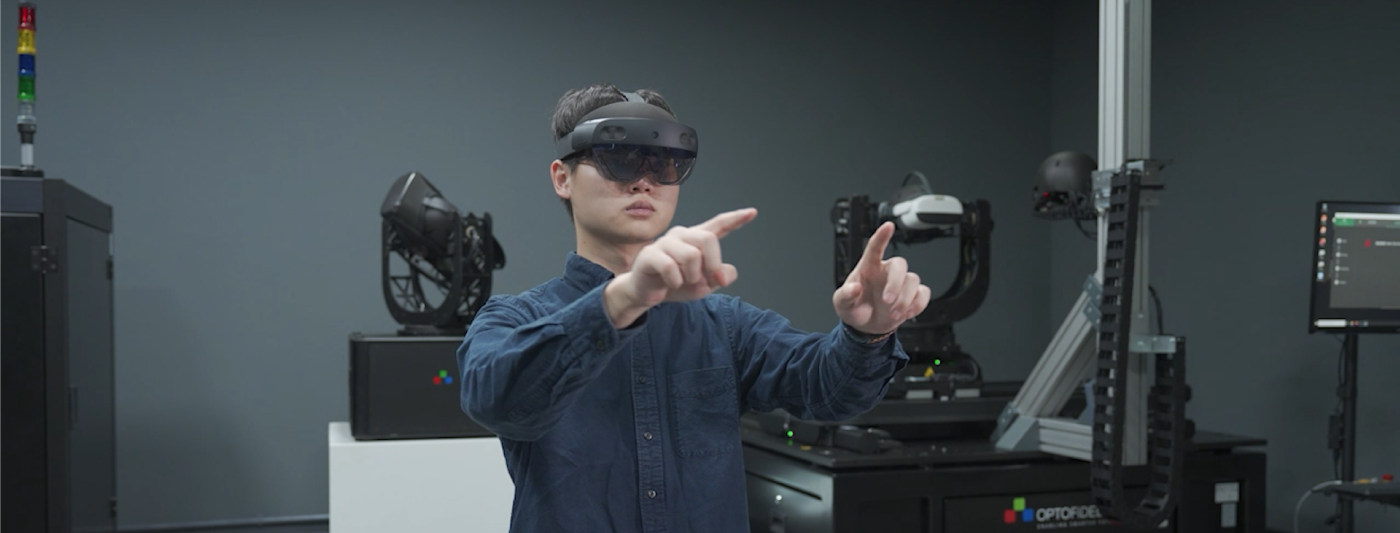
Improving AR Waveguide Image Quality with Precise Measurements and Grating Analysis
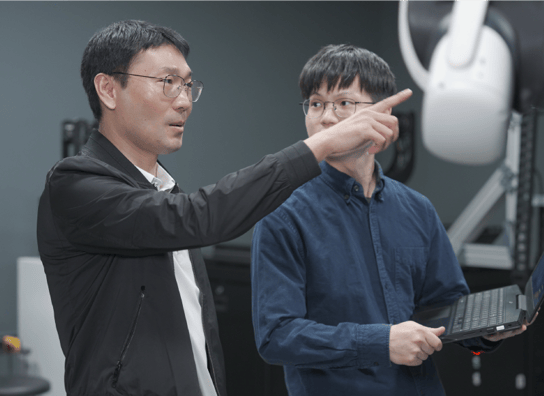
AR and MR glasses use waveguides to display the projected image on the lens. The quality of the waveguides largely determines the image quality of AR glasses. Due to the high-precision optics required, designing and manufacturing AR glasses with crisp image quality is extremely challenging. By using OptoFidelity’s measurement systems, you can measure the image quality of your AR waveguides and improve the end-user experience.
Key Points of This Use Case
- Accurate image quality measurements help design and manufacture AR/MR glasses with vibrant colors and high contrast.
- OptoFidelity’s measurement systems reduce R&D cycles and provide reliable measurements.
- When used together, WG-IQ and WG-GAT provide a platform for analyzing and improving waveguide image quality.
The Purpose of AR Waveguides
Waveguides are physical structures used to control the path of light. Their small size enables the design of compact augmented reality (AR) and mixed reality (MR) smart glasses instead of bulkier optical solutions.
Waveguides in AR smart glasses are critical in displaying information to the user. Unlike VR headsets with built-in displays, AR and MR glasses and headsets use projectors to cast the image into a transparent waveguide made of glass or plastic.
Optical waveguides trap the light from the projector and display the image to the user. Diffraction gratings are tiny structures within the waveguide that enable precise control over the light propagation. Their quality is essential to good image quality.
Challenges in Creating the Perfect Waveguides
Perfecting waveguides is a challenge for most designers and manufacturers of AR/MR smart glasses. The glasses are tiny devices that have strict weight and form-factor limitations if they are to appeal to a mass market audience. Reaching a satisfactory optical quality within these limitations is hard.
Designers try to simulate image quality by changing waveguide materials, material properties, and design. The waveguides come to life in prototypes, which undergo image quality measurements. Currently, many R&D teams use self-engineered measurement setups. The manual tests slow down the iterative design process.
These tests measure image quality but do not offer insights on what needs to be improved. We need to also consider the manufacturing quality of the waveguides.
In addition, designing a high field-of-view imaging system suitable for measuring the image quality like the human eye would see them is demanding.
The Quality Factor of Waveguides
The quality factor of waveguides is essential to ensuring good image quality. Poor waveguide grating quality results in poor image quality, simple as that.
Manufacturing the waveguides – even the prototypes – requires several manufacturing phases. Each phase has extremely strict tolerances for error. The easiest way to pinpoint errors in the production is to measure the results of each waveguide production phase.
Getting the quality factor of waveguides correct requires high-precision tools that document how well each manufacturing phase succeeded in producing exactly the waveguide that was designed. Ensuring high-quality manufacturing is essential for validating waveguide designs in R&D phase. True comparison between designs is only possible by ruling out that possible inferior image quality is not caused by manufacturing. High manufacturing quality is also the first key step towards enabling mass production of AR glasses.
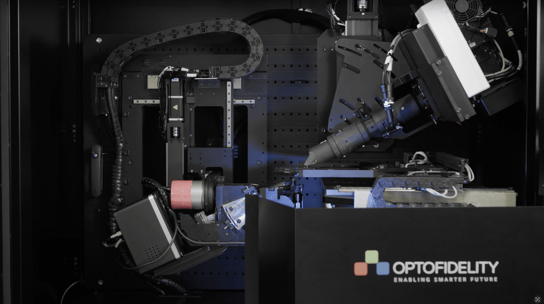
Measuring AR Waveguide Image Quality
OptoFidelity WG-IQ is a fully automated system for measuring and testing waveguide image quality. Designers don’t have to go back and forth to adjust measurement instrument angles and positions between tests, as WG-IQ handles the comprehensive test automatically. This enables measuring different angles and eye-box locations, providing automatically analyzed results. This radically speeds up testing,reduces time-to-market, and most importantly, provides a traceable baseline for image quality measurements
Learn more about OptoFidelity WG-IQ
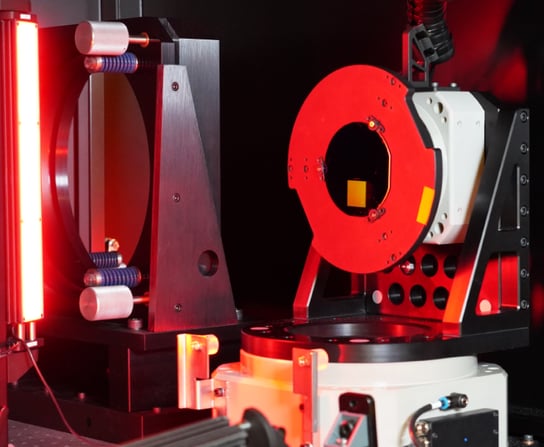
Characterizing AR Waveguide Grating Quality
Traditionally, waveguide grating are characterized using microscopes. However, their accuracy is not enough when looking at very minute details in the gratings.
OptoFidelity WG-GAT is an automated waveguide grating test system. The high-accuracy diffractometer tells you whether the waveguide is manufactured up to the precise standards, eliminating uncertainty on whether manufacturing quality is good enough. Instead of a microscope, WG-GAT uses a laser to reliably measure the quality down to the atomic level.
As there are several phases to manufacturing waveguides, WG-GAT can be used in every manufacturing phase to really understand the phases causing the biggest quality issues.
Using WG-IQ and WG-GAT together to improve AR image quality
There is no perfect R&D process but using OptoFidelity WG-IQ and WG-GAT together can certainly get you closer to perfection. WG-IQ tells you how good the image quality is. WG-GAT then links any shortcomings in image quality to the waveguide manufacturing process. As a result, you can efficiently create AR and MR waveguides with outstanding image quality.